Due to the numerous rules and recommendations for
installation in the bearing area, the external dimensions of the different ball bearing manufacturers differ only in nuances. The large differences are evident
in the internal values of the ball bearing, the materials used for the rings
and seals, the number of balls and their diameter, the surface structure and
the precision of the profile, as well as the lubricant used.
350,000 RPM separable ball bearing GRW has, as required,
three different materials to choose from for ball bearing rings. You can choose
between 100Cr6, X65Cr13 (SS) or X35CrMoN15-1 (SV30).
Regardless of whether the customer's focus is on hardness, operating temperature or corrosion resistance, in the hardening process developed by GRW, the desired properties can be specifically invoked and implemented in the internal hardening workshop. In order to obtain additional functional properties of the bearing ring, coatings can also be provided.
Steel Tumbling Media, catalyst balls, forged steel grinding balls, forged steel balls, ceramic grinding media suppliers, Steel Tumbling Media, zirconium silicate beads, catalyst bed support balls
Regardless of whether the customer's focus is on hardness, operating temperature or corrosion resistance, in the hardening process developed by GRW, the desired properties can be specifically invoked and implemented in the internal hardening workshop. In order to obtain additional functional properties of the bearing ring, coatings can also be provided.
Steel Tumbling Media, catalyst balls, forged steel grinding balls, forged steel balls, ceramic grinding media suppliers, Steel Tumbling Media, zirconium silicate beads, catalyst bed support balls
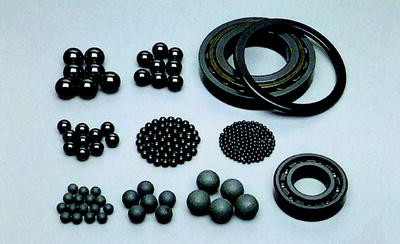
In addition, the most recent procedures are used through PVD
(physical vapor deposition) or CVD (chemical vapor deposition) and meet the
highest standards of coating quality. An unwanted dissolution of the coating
will result in a serious early bearing failure. Therefore, all coating
varieties are subject to strict GRW standards and quality tests.
Torlon Snap Retainer The retainer must hold the balls at the
same distance from each other and avoid touching each other. In addition, the
retainer must have an appropriate design with defined material strengths and
balanced elasticity, to withstand the ball bearing load as well as possible.
In addition to the strict tolerance specifications for GRW
ball bearing rings with respect to surface finish, shape accuracy and steel
purity, the same requirements apply to the design and production of the
retainer. There are 3 basic variants for retainers: inner ring, outer ring or
ball-controlled retainer.
These basic types can be combined with 21 different
materials. The material selection covers the entire range, from metal tapes for
steel tape retainers to special aviation and spaceflight materials, to
chemically coupled “PAI - PTFE-cg” plastic for heavy applications for
applications with the most high standards of wear behavior, temperature
resistance and sterilization capacity.
grinding balls, milling media, shot peening media, grinding media, stainless steel tumbling media,steel tumbling media, alumina grinding balls, zirconium oxide beads
grinding balls, milling media, shot peening media, grinding media, stainless steel tumbling media,steel tumbling media, alumina grinding balls, zirconium oxide beads
Lubricants serve to reduce friction and wear, as well as
cooling, shock absorption, sealing effect and corrosion protection. Lubrication
can be carried out using greases or oils and / or in special cases solid
lubricants. All 3 types are recovered in GRW products. The installation
situation of the ball bearing is crucial for the selection of a suitable
lubricant. Grease lubrication is recommended for general use at low to medium
speeds and, therefore, is the most commonly used type of lubrication. The main
part of the lubricating grease consists of base oil and the smallest part
consists of the appropriate thickener. The lubrication of the bearings is
mainly done with base oil, which releases the thickener in small amounts over
time. GRW uses lime soaps, natron soaps, lithium soaps and complex soapy fats.
Oil lubrication is used if grease lubrication cannot be used
for technical or economic reasons. This may be the case with high operating
temperatures, caused by ambient temperature or frictional heat in the ball
bearing. The oils are divided into mineral and synthetic oils. Animal or
vegetable oils are not suitable or only suitable to some extent for use in ball
bearings. In total, more than 400 lubricants are used in GRW and, therefore,
cover a large area of use, from the food industry to aviation and
spaceflight.
Various types of shileds in ball bearings Finally, the
shield is mounted on the ball bearing as the last component. This should keep
the impurities away from the high precision functional surfaces of the bearing
and, therefore, produce as little friction as possible. On the other hand, this
should keep the lubricant in the bearing. Impurities that get between the ball
and the raceway will tip over and damage the processed tracks. To avoid this,
contactless protectors and contact protectors are offered, with various sealing
qualities.
carbon steel balls, chrome steel balls, stainless steel media, stainless media, zirconium beads
carbon steel balls, chrome steel balls, stainless steel media, stainless media, zirconium beads
With contactless protectors there is no increase in torque,
since the protector creates a separation ring. It does not produce friction
and, therefore, can be used even at the highest speeds.
With the contact protector, the so-called ball bearing seal
touches the shoulder of the inner ring with a defined contact pressure and,
therefore, causes a greater moment of friction. Compared to contactless
protectors, all contact protectors will wear out over time. Dust protectors are
mainly produced from stainless steel or Perbunan rubber reinforced with steelsheets. The established seals are made of a fiberglass reinforced Teflon disc
or a synthetic fluorine rubber reinforced with steel sheets. In total there are
63 shield variants to choose from.
alumina ball, bead media, glass bead media, catalyst media, stainless steel balls
alumina ball, bead media, glass bead media, catalyst media, stainless steel balls
At GRW, individual products are made of these components for
the customer's special requirements. Due to a sensible combination strategy of
standard and special components, GRW can satisfy the most diverse market requirements
and guarantee our customers a competitive advantage.
The extensive and competent advice and design of a ball bearing are the prerequisites for the highest compliance with the established
requirements. Even in the development phase of new applications, GRW engineers
can provide valuable technical information and, for the most part, also cost
savings.